Aerospace & Defense
Companies involved in the design, manufacture, and deployment of aerospace and defense components and products have a significant need to protect their mission-critical work. Dycem’s aerospace cleanrooms support leaders in the industry by offering an effective process improvement to dramatically reduce contamination and the damage it can cause.

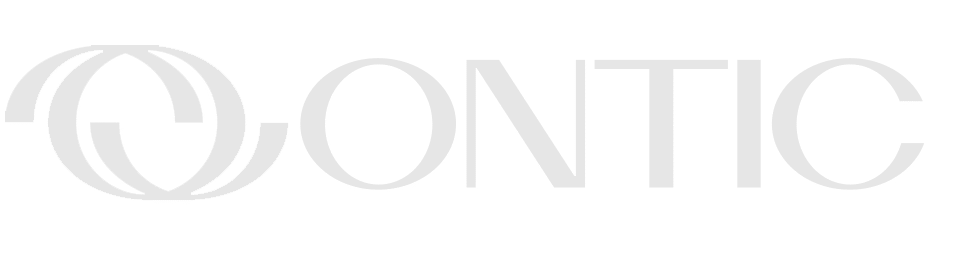
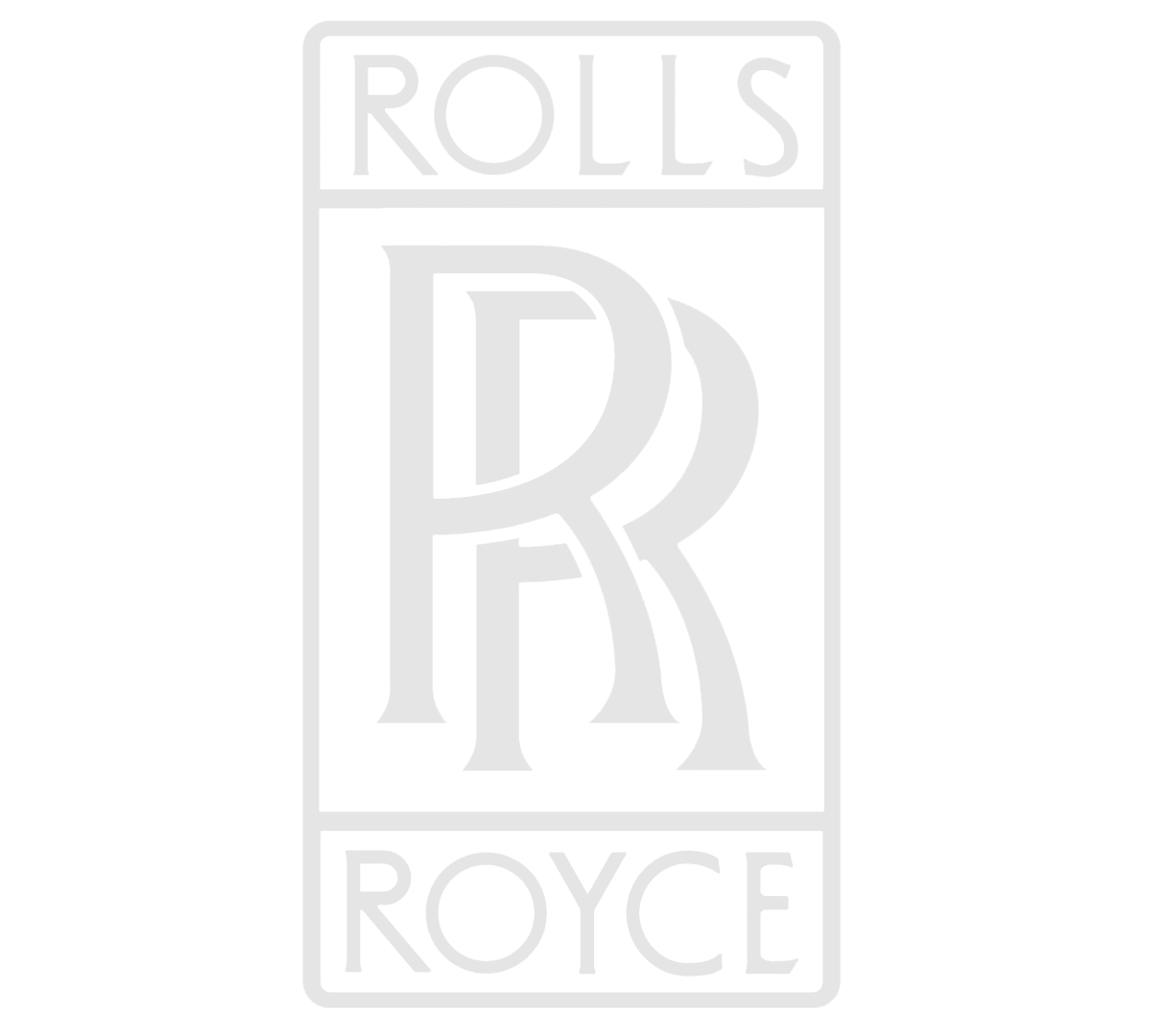
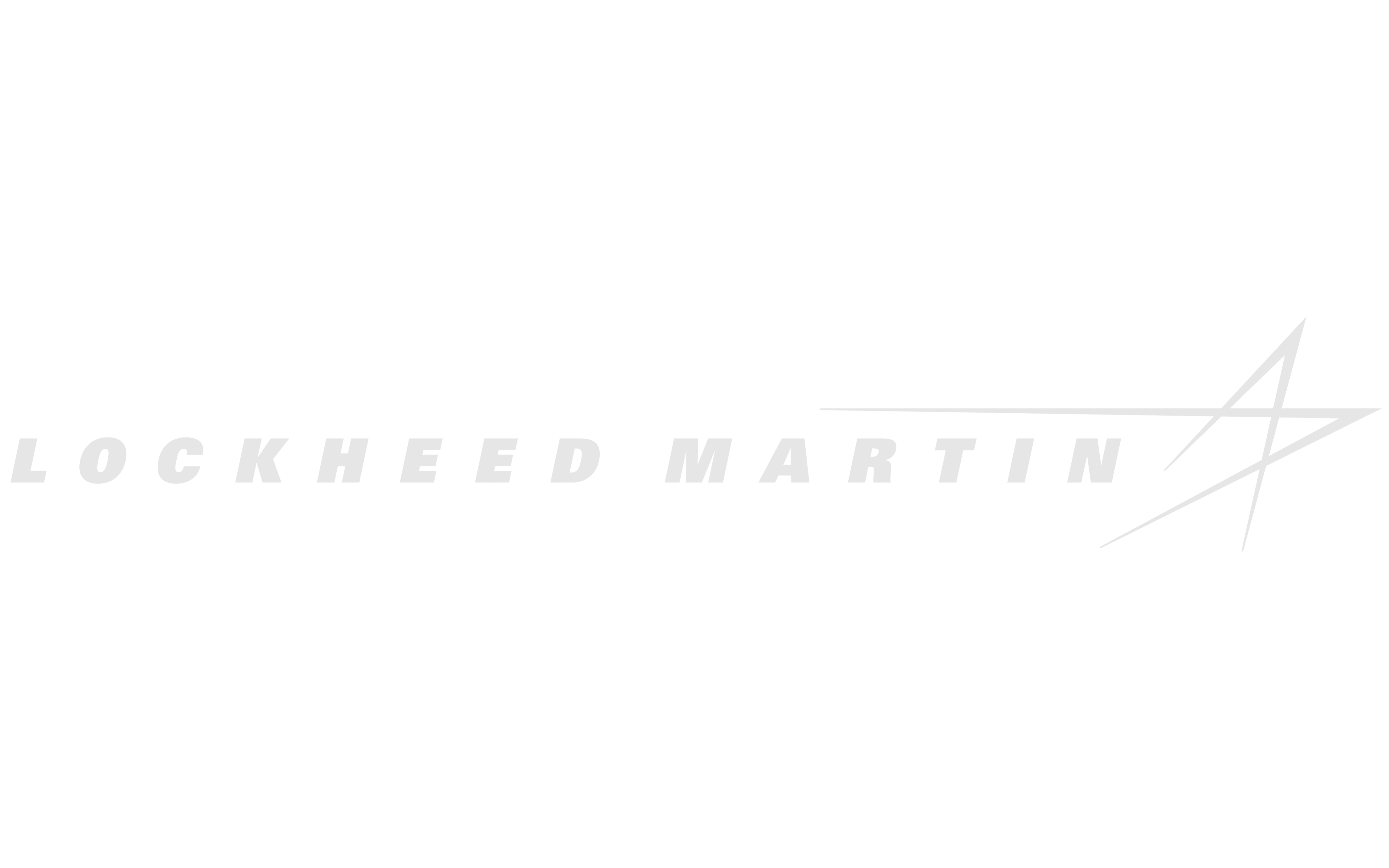
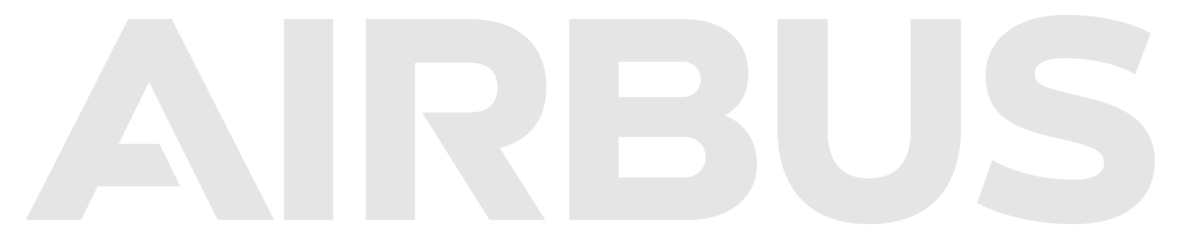
Where to use Dycem in Aerospace
Entry and Exit to Cleanrooms.
Paint Areas.
Small Components Areas.
Assembly Areas.
ESD Zones.
Engine Laboratories.
Display and Glass Manufacturing.
Contamination: The Risk in Aerospace & Defense
Contamination control has become a growing concern in aerospace and defense manufacturing. The harmful effects posed by contamination threaten innovative developments and advancements within the industry. The use of aerospace cleanrooms and controlled spaces helps to monitor and minimize the level of contaminants from personnel, equipment, and environmental factors, which is needed to produce safe and effective equipment.
Common types of contamination found within manufacturing include dust, debris, fibers, skin cells, static, and other particulate matter. The presence of these contaminants can cause several negative outcomes including degraded product performance, decreased product yield, rejected goods, and safety concerns.
The risks to a company’s brand, its profitability, and its people are too big to be ignored. Effective contamination control is essential for facilities in all processes throughout the fabrication, assembly, integration, and testing phases of operation.
Dycem mats, implemented as part of a contamination control strategy, offer optimal support in reducing the risk of contamination in aerospace and defense manufacturing. Dycem offers proven protection, collecting and retaining up to 99.9% of foot and wheel-borne contamination, and 75% of airborne contamination.
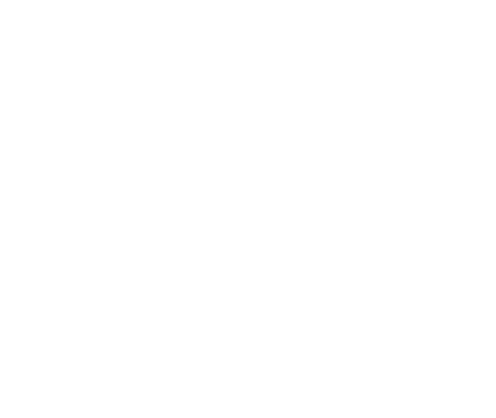
Don't Ignore the Floor...
80% of Contamination Enters a Critical Space at Floor Level.
Benefits of Dycem in Aerospace & Defense
superior particle collection & retention
Dirt and dust from shoes and wheels are captured on Dycem mats and remain on the surface until cleaned off. With Dycem, aerospace manufacturing areas and cleanrooms benefit from a reduction in floor-level particulate of up to 99.9% and a reduction in air particulate levels of up to 75%.
Reduced concerns of esd damage
With Dycem mats installed prior to critical areas, our aerospace customers have peace of mind that damage from an Electrostatic Discharge (ESD) occurrence will be minimized. All Dycem mats dissipate static at 10⁸ ohms.
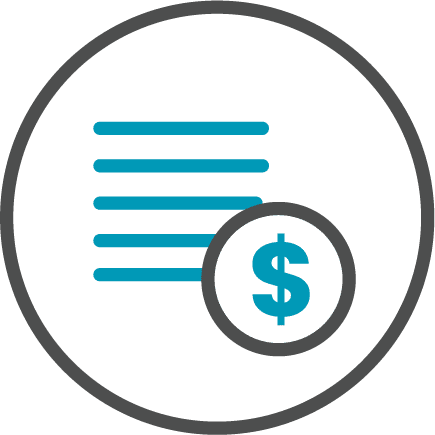
long-lasting & cost-effective
Unlike disposable contamination control solutions, Dycem mats last on average 3+ years. aerospace manufacturers typically see an ROI shortly after purchase, as well as the added benefit of a reduced carbon footprint.
Our Products, Your Industry
From protecting satellite manufacturing and testing to space vehicle assembly and circuit board configuration, Dycem has solutions to support the many complex products and processes in the aerospace and defense industry. Keeping contamination out of critical spaces and aerospace cleanrooms is our priority.
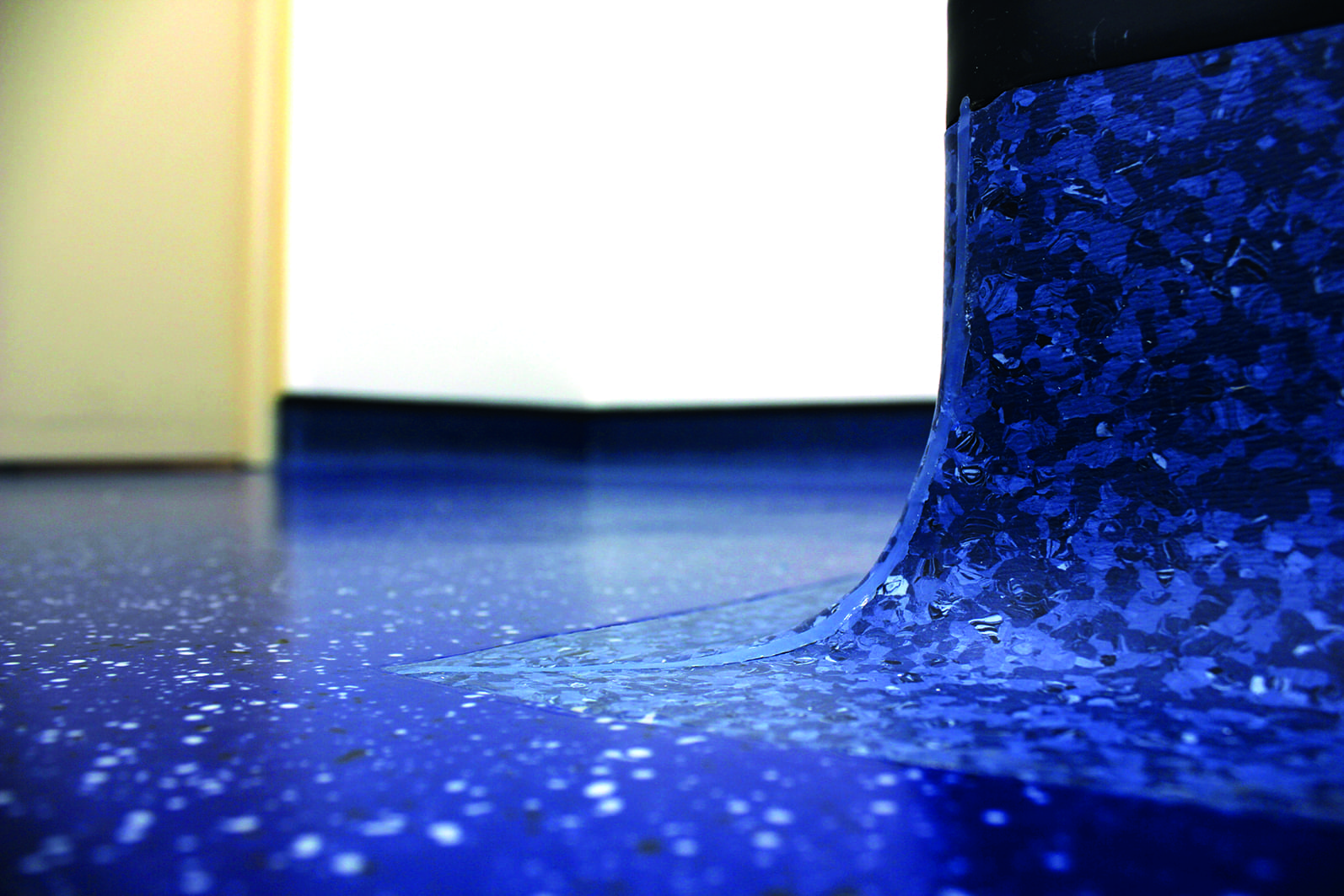
Dycem CleanZone
CleanZone helps control contamination from the shoes of personnel.
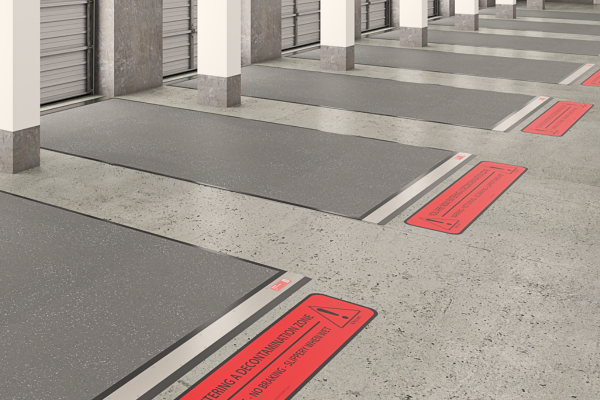
Dycem WorkZone
WorkZone is the only effective solution for decontamination of heavy wheels.
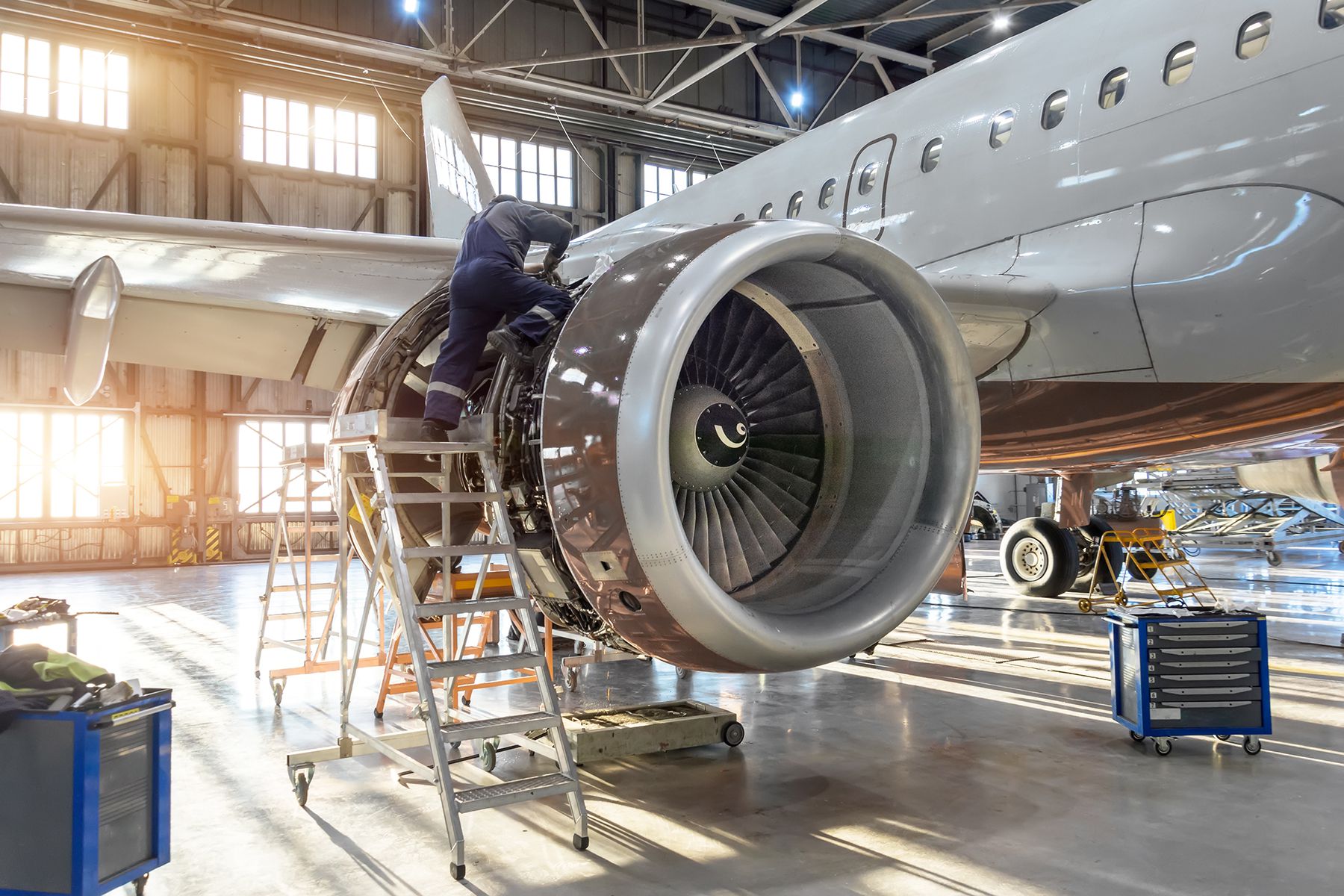
In Your Industry
Discover your industry’s specific applications—all conveniently summarized right here.
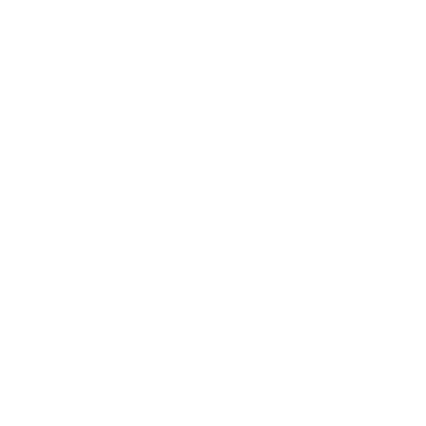
Success Stories...
Discover our success stories in your industry.
Learn how our customers have benefitted from installing Dycem.
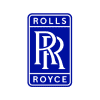
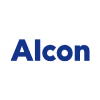
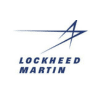
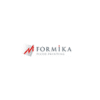
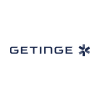
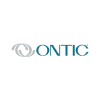
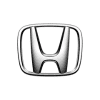

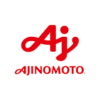
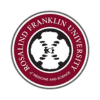
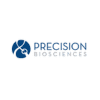
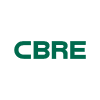
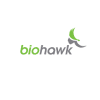
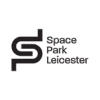
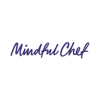
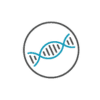
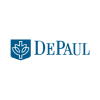
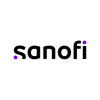
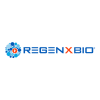
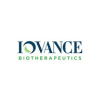
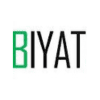
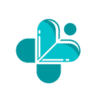
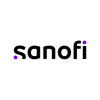
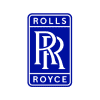
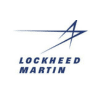
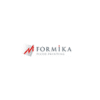
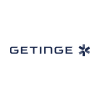
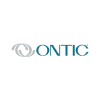
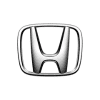

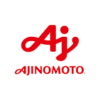
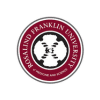
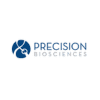
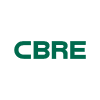
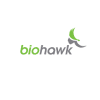
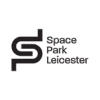
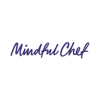
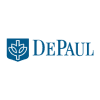
NASAs Contamination Control Engineering
Read the following quote from NASAs Contamination Control Engineering Design Guidelines for the Aerospace Community:
“4.1.4.3.4 Entering the Garment Room and Controlled Work Areas The purpose of the cleanroom garment is to protect hardware from contaminants generated by people. Cleanroom garments should be selected based on hardware cleanliness requirements and the types of operations that must be performed in the cleanroom. Smocks do not provide good isolation of hardware from people generated contaminants. Fibers from street clothes worn under the smock will fall out from under the smock. These fibers will generally be larger and will settle out of the air close to where they are generated. There may be places and operations in a cleanroom where this is acceptable, but only a full coverall will provide the required isolation when people are working in, around, and above spacecraft hardware. Requirements for entry into the garment room and controlled work areas include:
- Shoes should be cleaned with a cleaning machine and mats at entry. Additional shoe coveting may be required.
- Aerospace cleanroom garments should be donned in the anteroom. Caps should be worn to cover as much hair as possible.
- Beards and Mustaches should be covered. Do not groom hair in the smock room or controlled work areas.
- Garments should be inspected before donning to ensure they are clean, there are no tips or open seams and all fasteners are usable.
- Aerospace cleanroom garments should not be worn outside the controlled area and anteroom. When not being worn they should be stored according to institutions.”
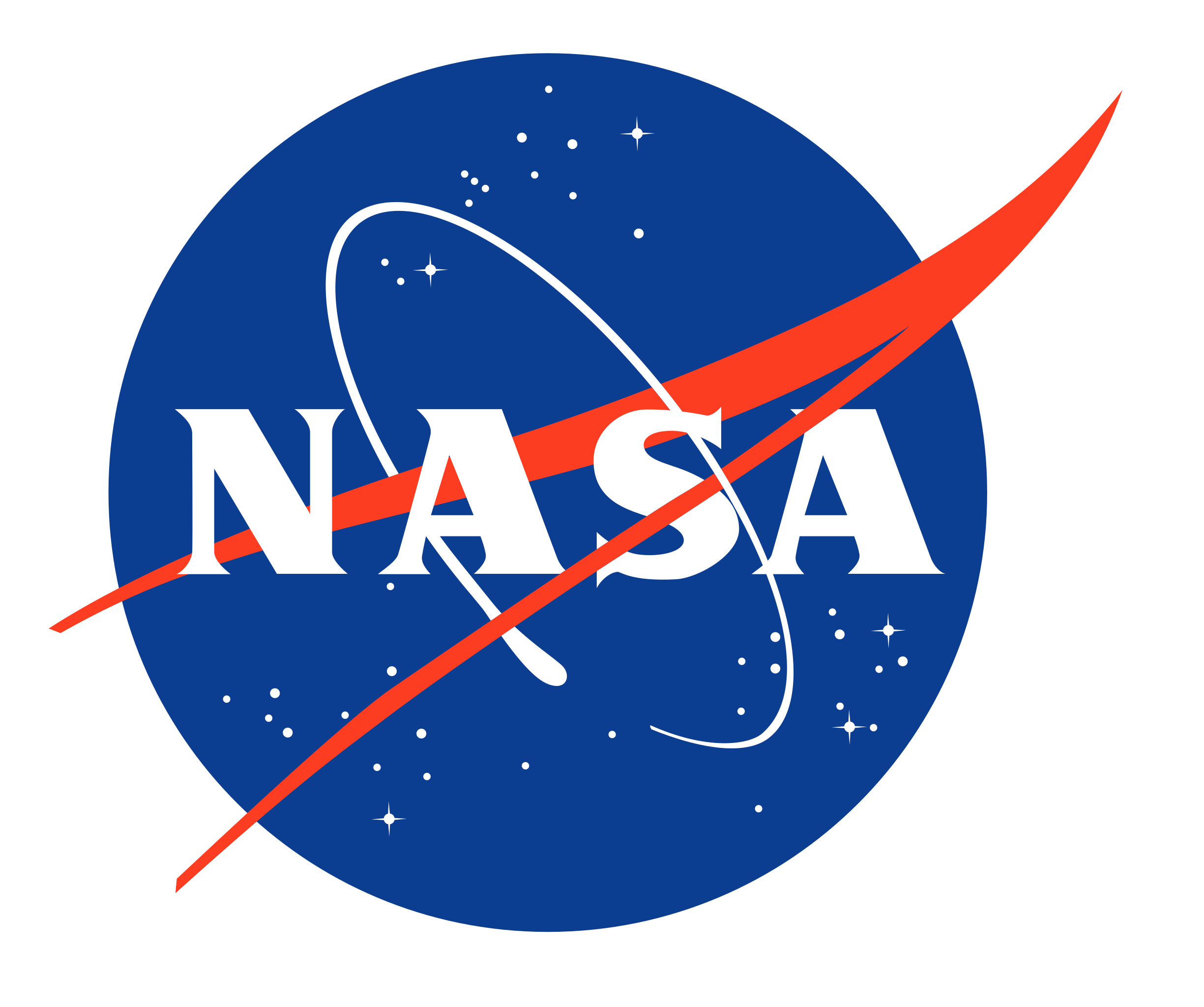