Electronics
With increasing complexity and a new era of excellence fueled by competition, the electronics industry must go to great lengths to protect its products from contamination. As a long-trusted partner to many of the industry leaders, Dycem products elevate production standards, safeguarding electronic components from harmful particles, and guaranteeing first-class performance and reliability in each device. We set a high standard in the industry of electronics cleanrooms.
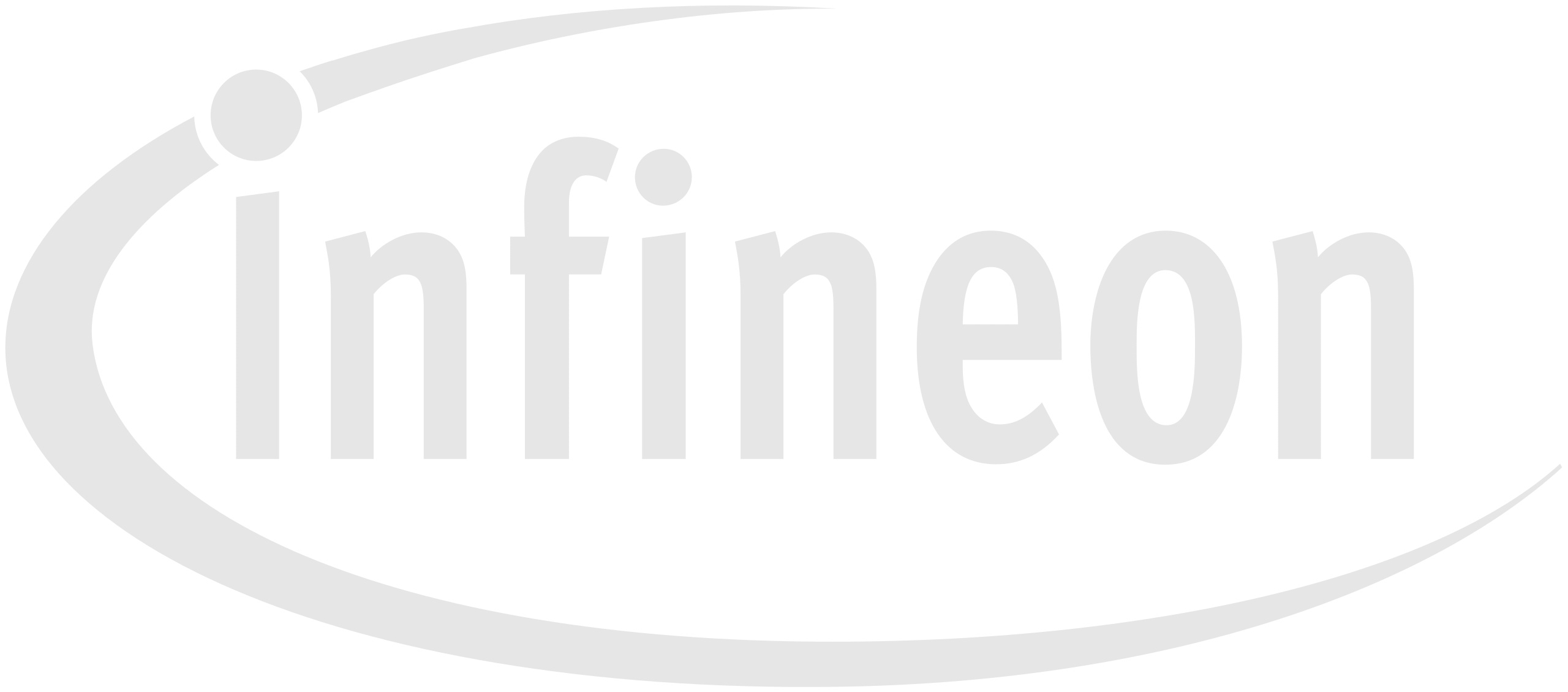
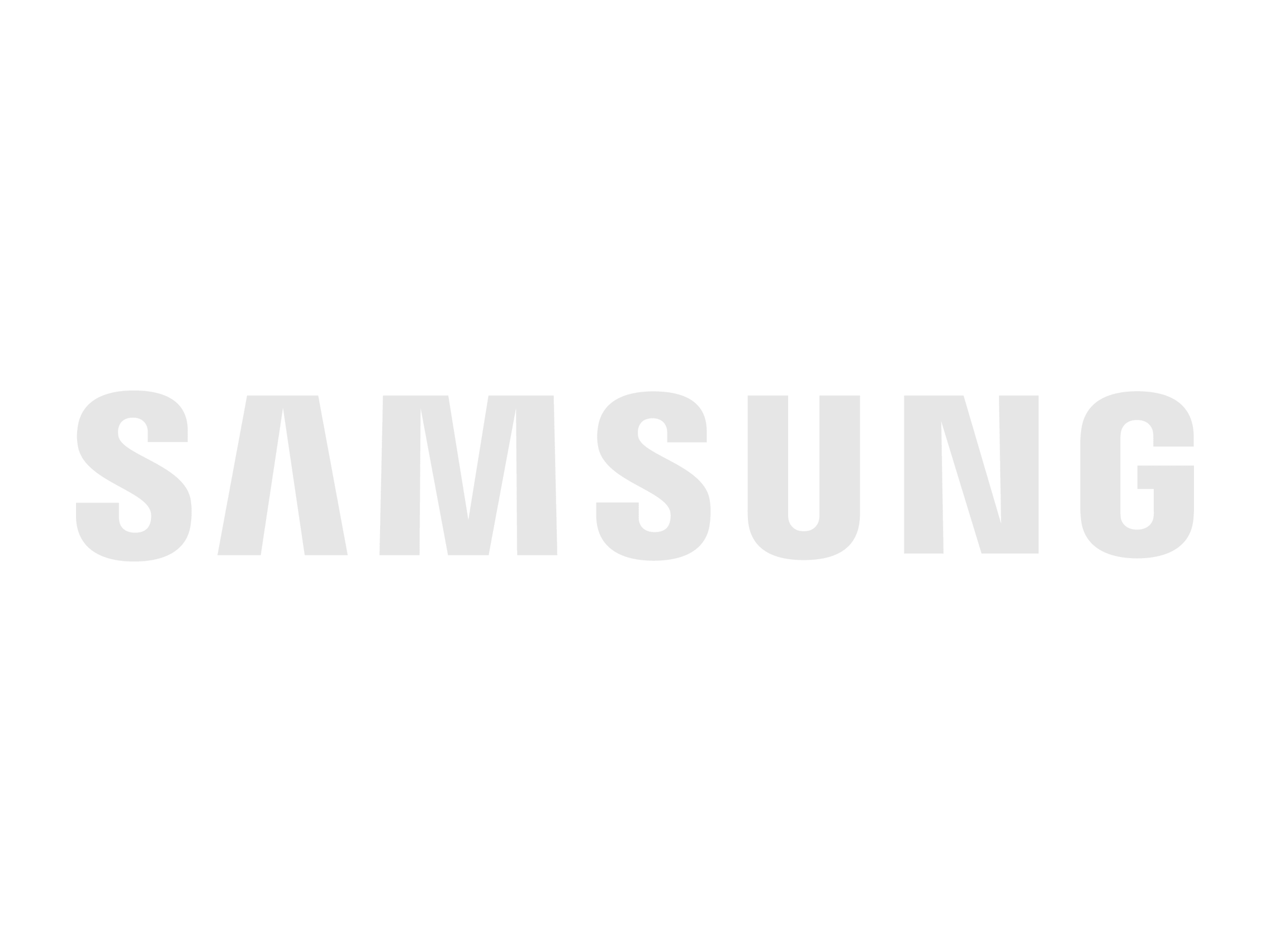
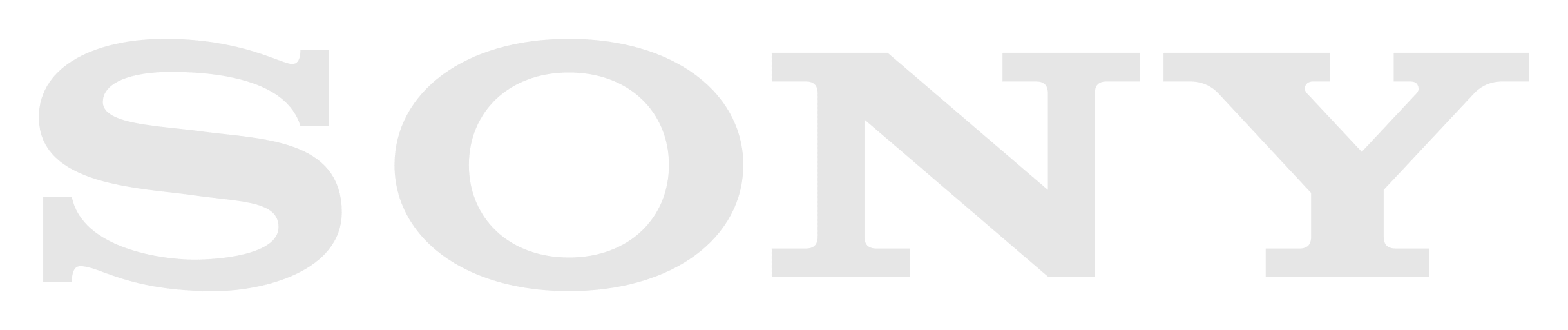
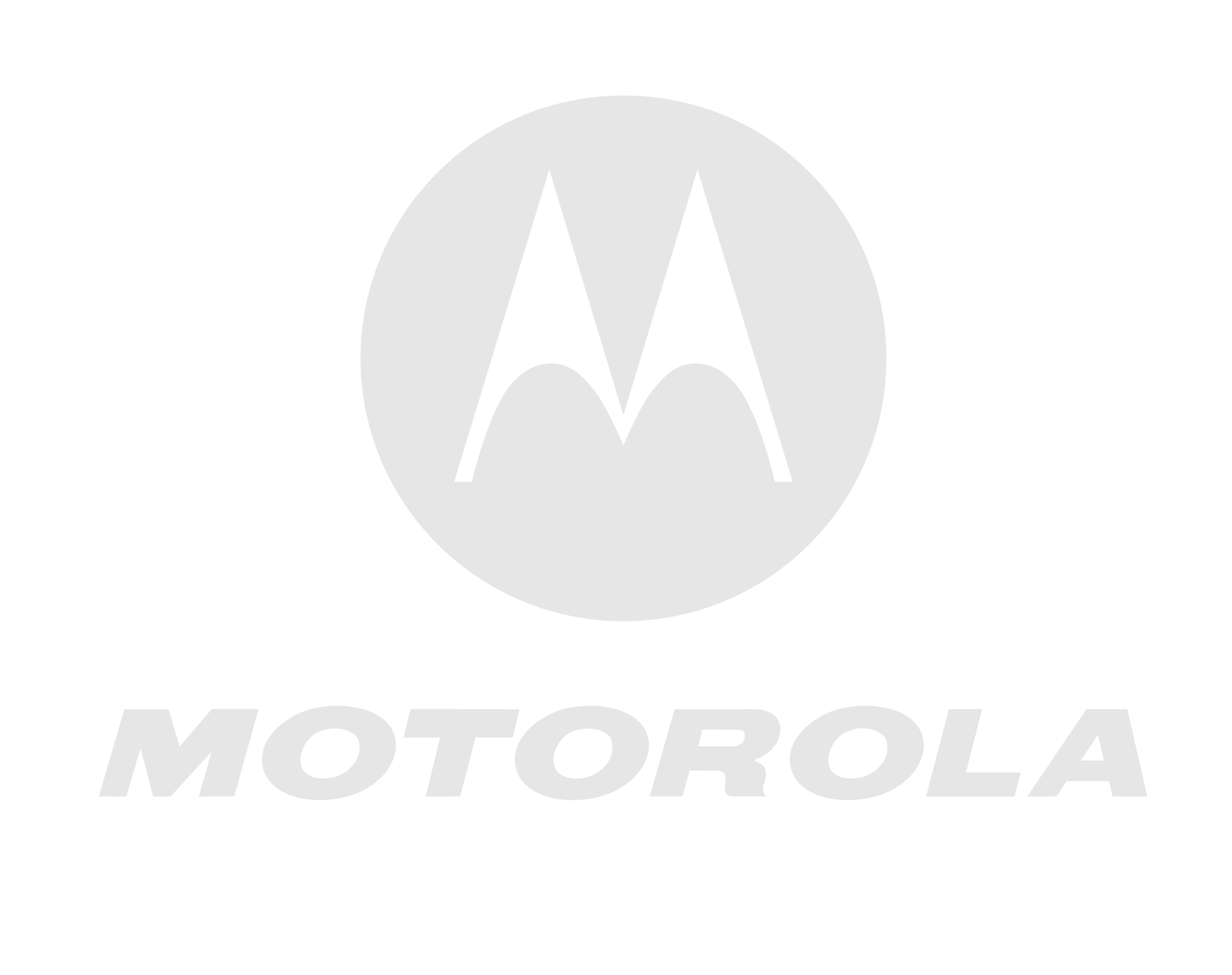


Where to use Dycem in Electronics
Entry and Exit to an Electronics Cleanroom.
Airshowers.
Component Assembly.
Goods In Areas.
ESD Zones.
Material Airlock Transfers.
Primary Packaging Zones.
Contamination: The Risk to the Electronic Industry
Contamination control has become a growing concern in many facets of the electronics industry, and a costly problem if unaddressed. The harmful effects posed by contamination threaten innovative developments and advancements within areas such as integrated circuits, microelectronics, and semiconductors, as well as embedded systems, photonics, and nanoelectronics. The use of an electronics cleanroom and controlled spaces helps to monitor and minimize the level of contaminants from personnel, equipment, and environmental factors.
Common types of contamination found in the design, manufacturing, assembly, and testing of electronics include dust, debris, fibers, skin cells, static, and other particulate matter. The presence of these contaminants can cause several negative outcomes including inferior quality and performance, unreliable products, decreased product yield, and safety concerns from product failure.
The risks to a company’s brand, its profitability, and its people are too great to be ignored. Effective contamination control is essential for facilities in all processes throughout the various phases of operation. This is why an electronics cleanroom is the future of the electronics industry.
Dycem mats, implemented as part of a contamination control strategy, offer optimal support in reducing the risk of contamination.
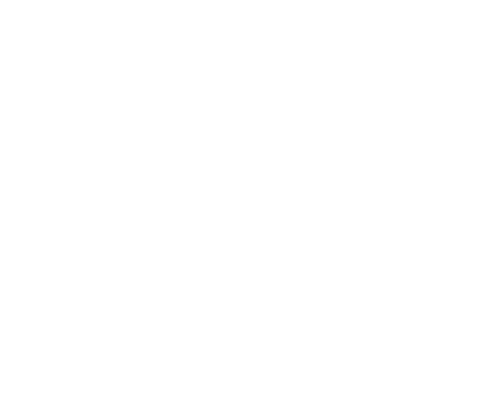
Don't Ignore the Floor...
80% of Contamination Enters a Critical Space at Floor Level.
Benefits of Dycem in the Electronics Industry
superior particle collection & retention
Dirt and dust from shoes and wheels are captured on Dycem mats and remain on the surface until cleaned off. Dycem mats help to reduce contamination from shoes and wheels by up to 99.9%, and airborne contamination by up to 75%, keeping unwanted particles out of cleanrooms and controlled spaces.
Reduced concerns about esd damage
With Dycem mats installed prior to an electronics cleanroom, our electronics customers have peace of mind that damage from an Electrostatic Discharge (ESD) occurrence will be minimized. All Dycem mats dissipate static at 10⁸ ohms.

Long-lasting, cost-effective Alternative
Unlike common disposable contamination control solutions, Dycem mats last on average 3+ years. Electronics manufacturers can expect an ROI shortly after purchase, as well as the added benefit of a reduced carbon footprint from less plastic waste.
Our Products, Your Industry
From prototyping and testing to mass production, all stages of the process run the risk of exposing electronic components and devices to possible detrimental contamination. Dycem has solutions to support the many complex and highly valuable products and processes in the electronics industry. Keeping contamination out of critical spaces and an electronics cleanroom is our priority.
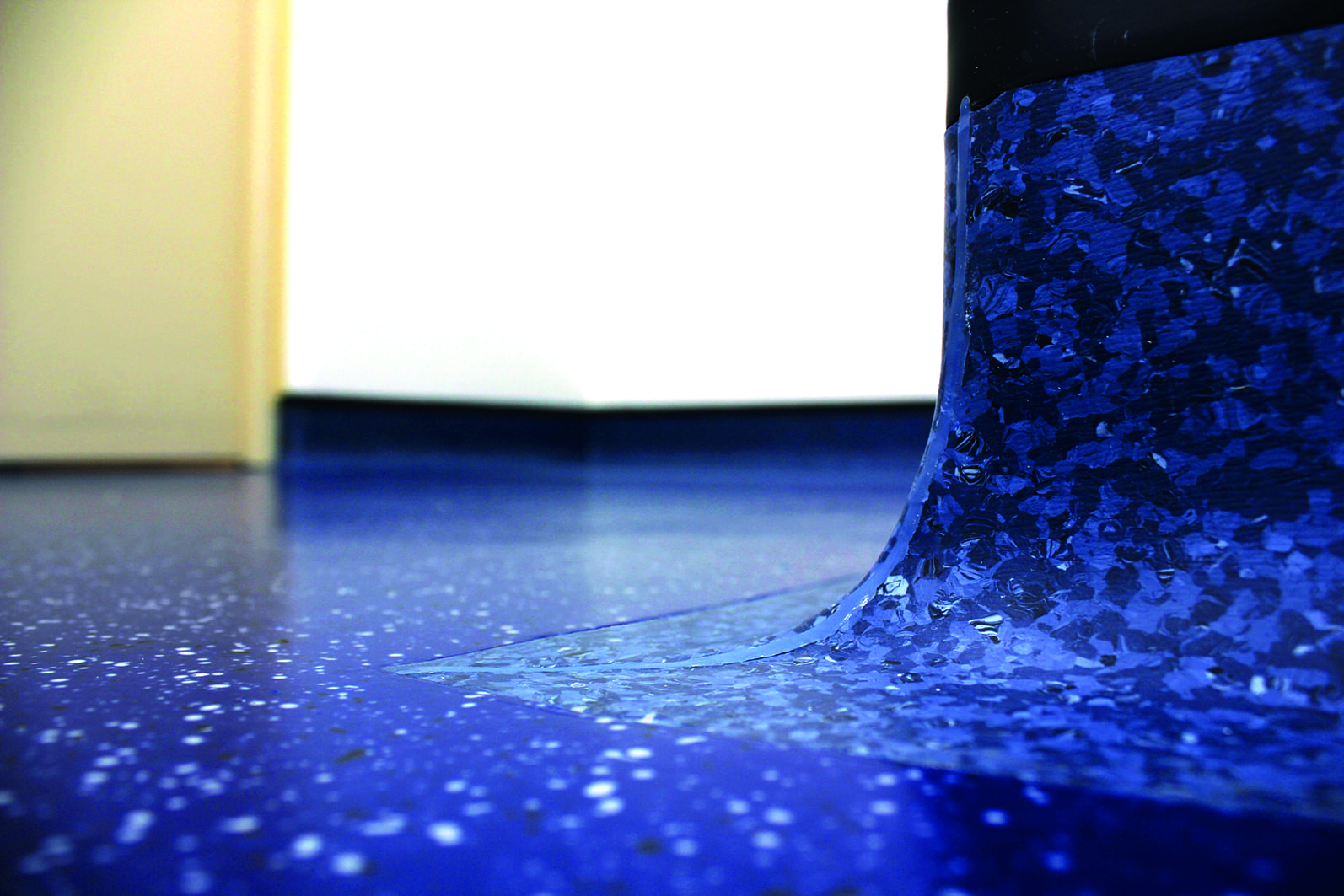
Dycem CleanZone
CleanZone helps control contamination from the shoes of personnel.
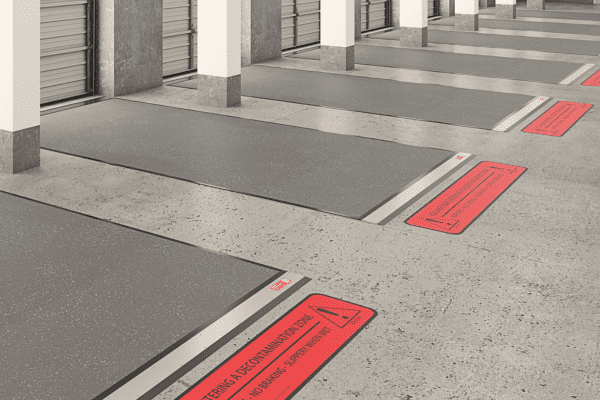
Dycem WorkZone
WorkZone is the only effective solution for decontamination of heavy wheels.
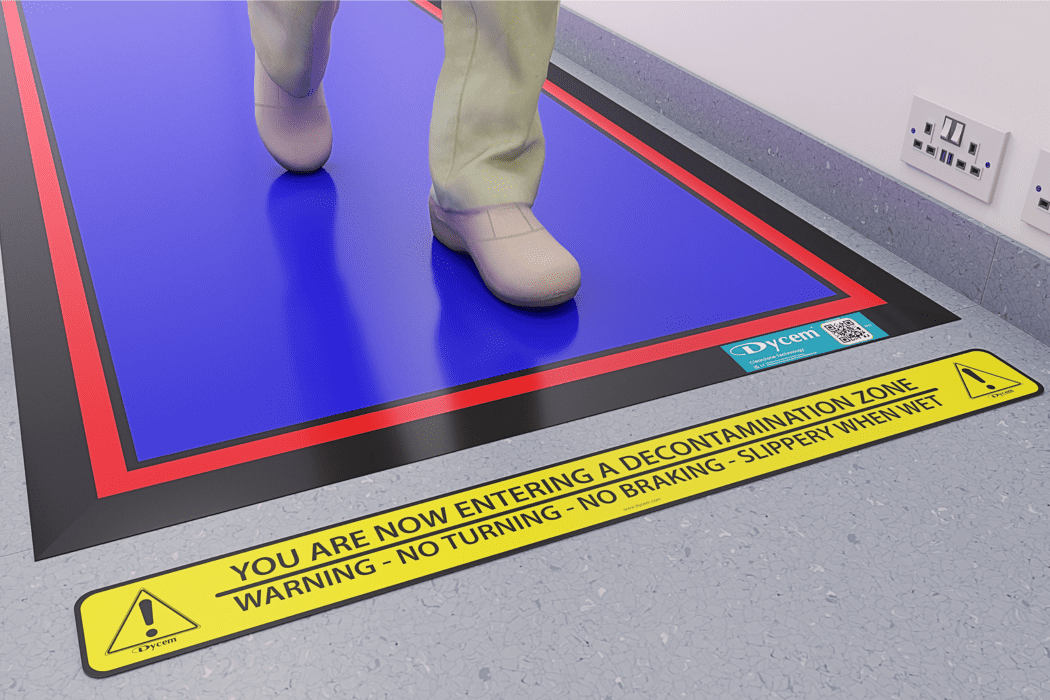
Dycem Floating Mats
Floating Mats are a contamination control solution that can be moved as needed.
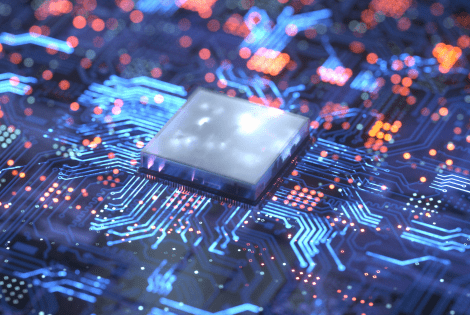
In Your Industry
Discover your industry’s specific applications—all conveniently summarized right here.
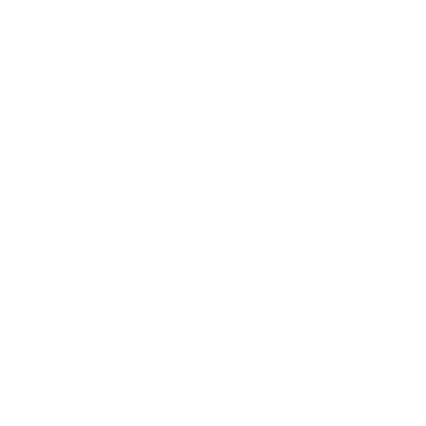
Success Stories...
Discover our success stories in your industry.
Learn how our customers have benefitted from installing Dycem mats in their electronics cleanroom.
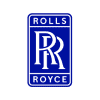
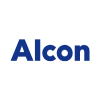
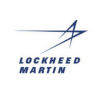
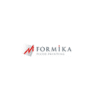

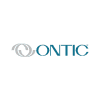
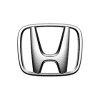
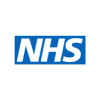
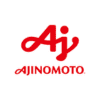
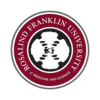
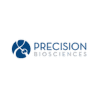

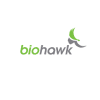
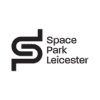
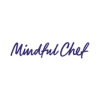
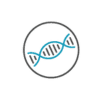
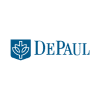
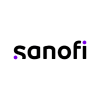
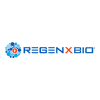
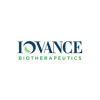
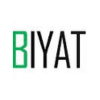
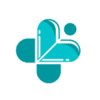
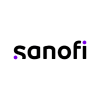
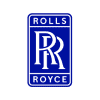
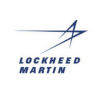
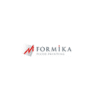

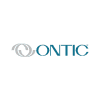
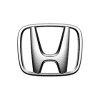
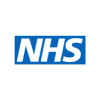
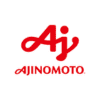
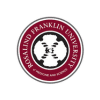
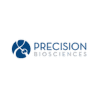

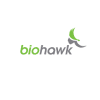
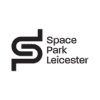
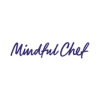
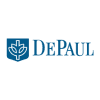
Maintaining a Mission Critical Mindset
Here is a great quote from Power Electronics News:
“Keep in mind that electronics may go into all kinds of devices, including some where consistency is mission-critical. For instance, air compressor cleaning is crucial for PCBs used in robotics development, including competitive robotics and aerospace robotics. Poor quality and performance consistency could result in a NASA rover glitching on Mars or a robotics competition ending up skewed due to a contaminated PCB.
To prevent incidents like these from happening, manufacturers need to use an electronics cleanroom and treat every component like it’s mission-critical. Using the best cleaning solutions and tools available, as well as a clear cleaning regimen, will ensure every electronic component ships out with the best quality and performance possible.”