Automotive
Companies involved in producing, assembling, finishing, and testing vehicles or their components have a responsibility to the end user to ensure the functionality and safety of their products. As a partner to many of the industry leaders, Dycem helps companies meet strict automotive contamination control requirements by reducing potentially harmful contamination within the manufacturing environment.
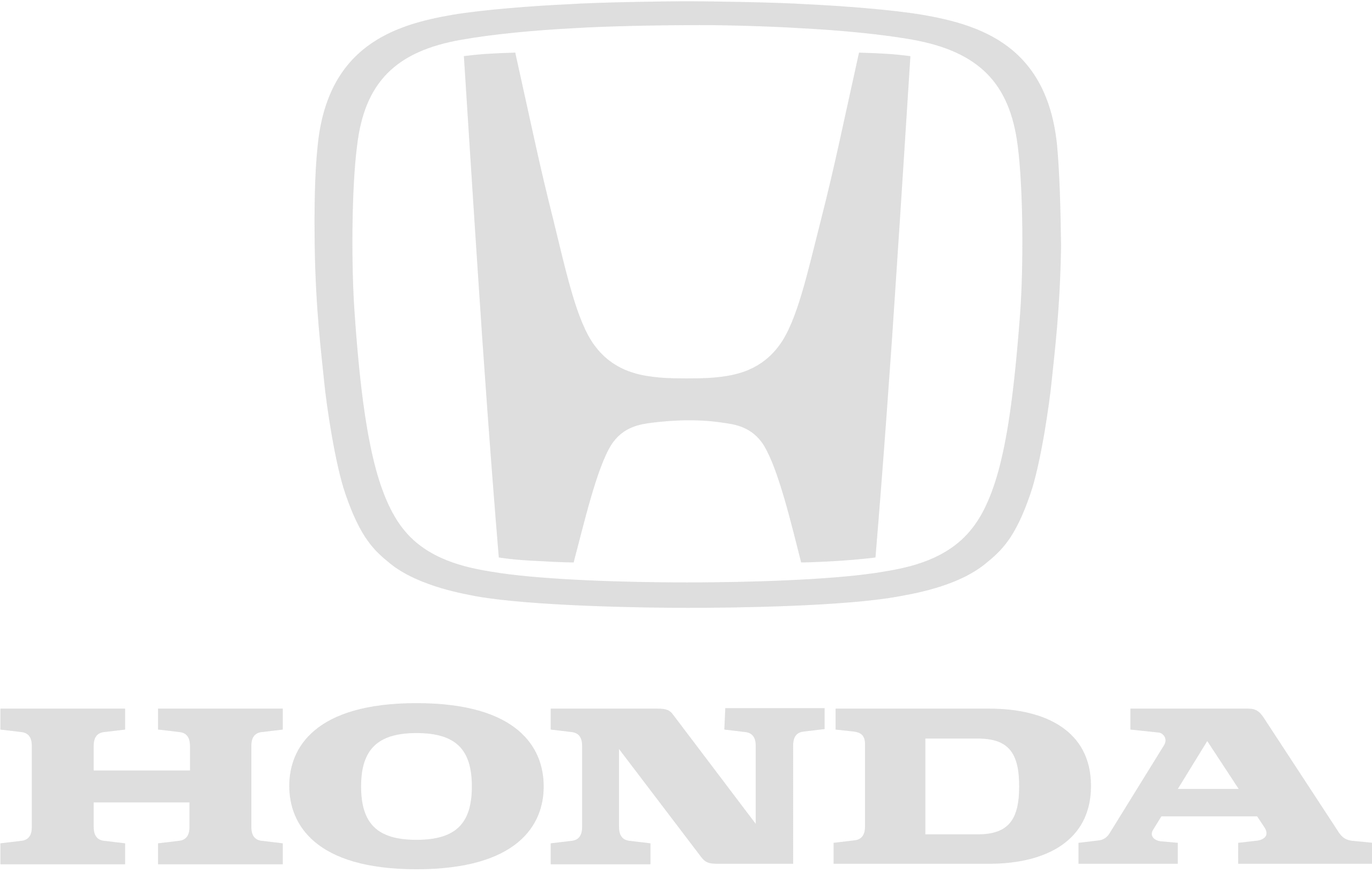
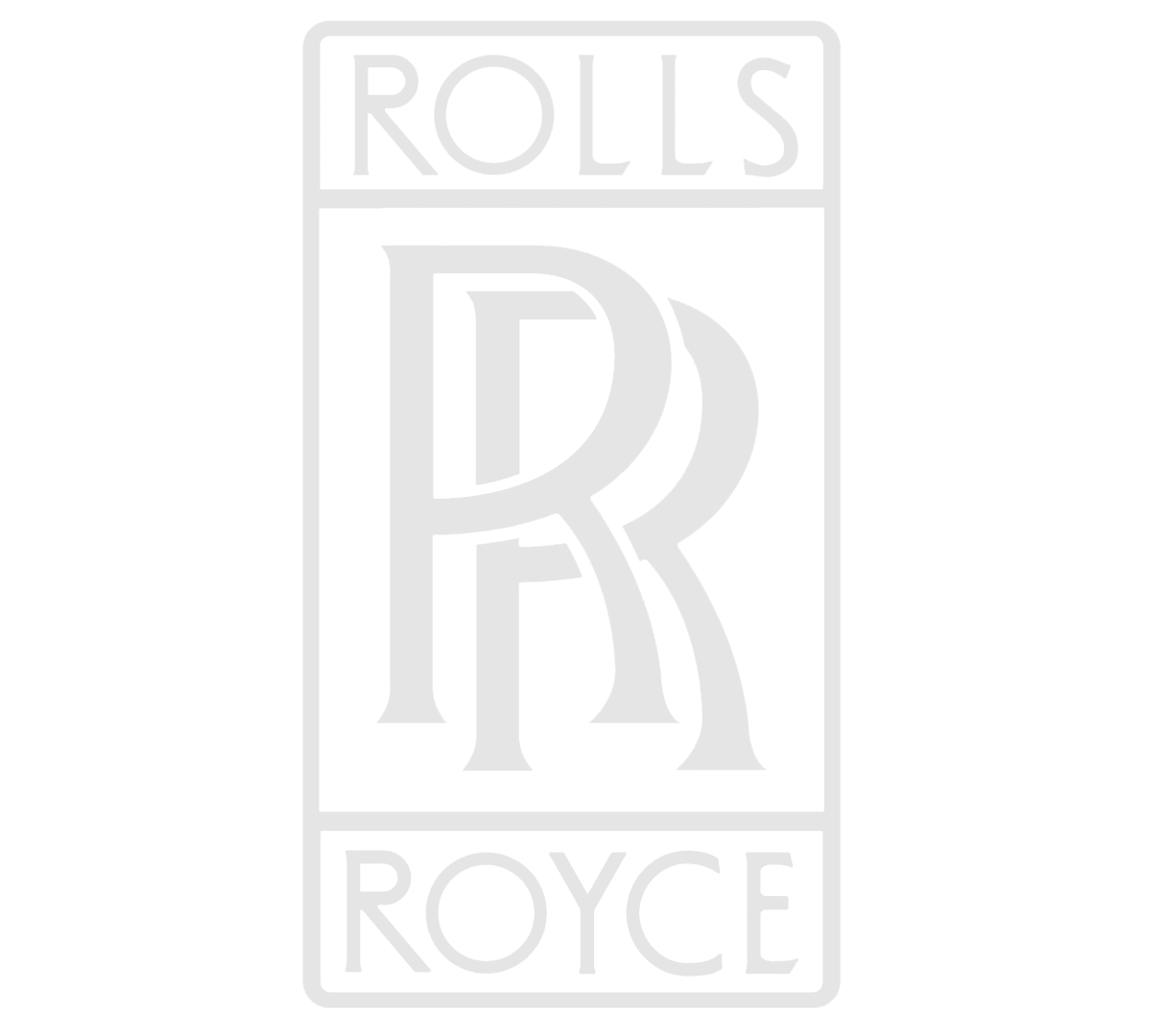
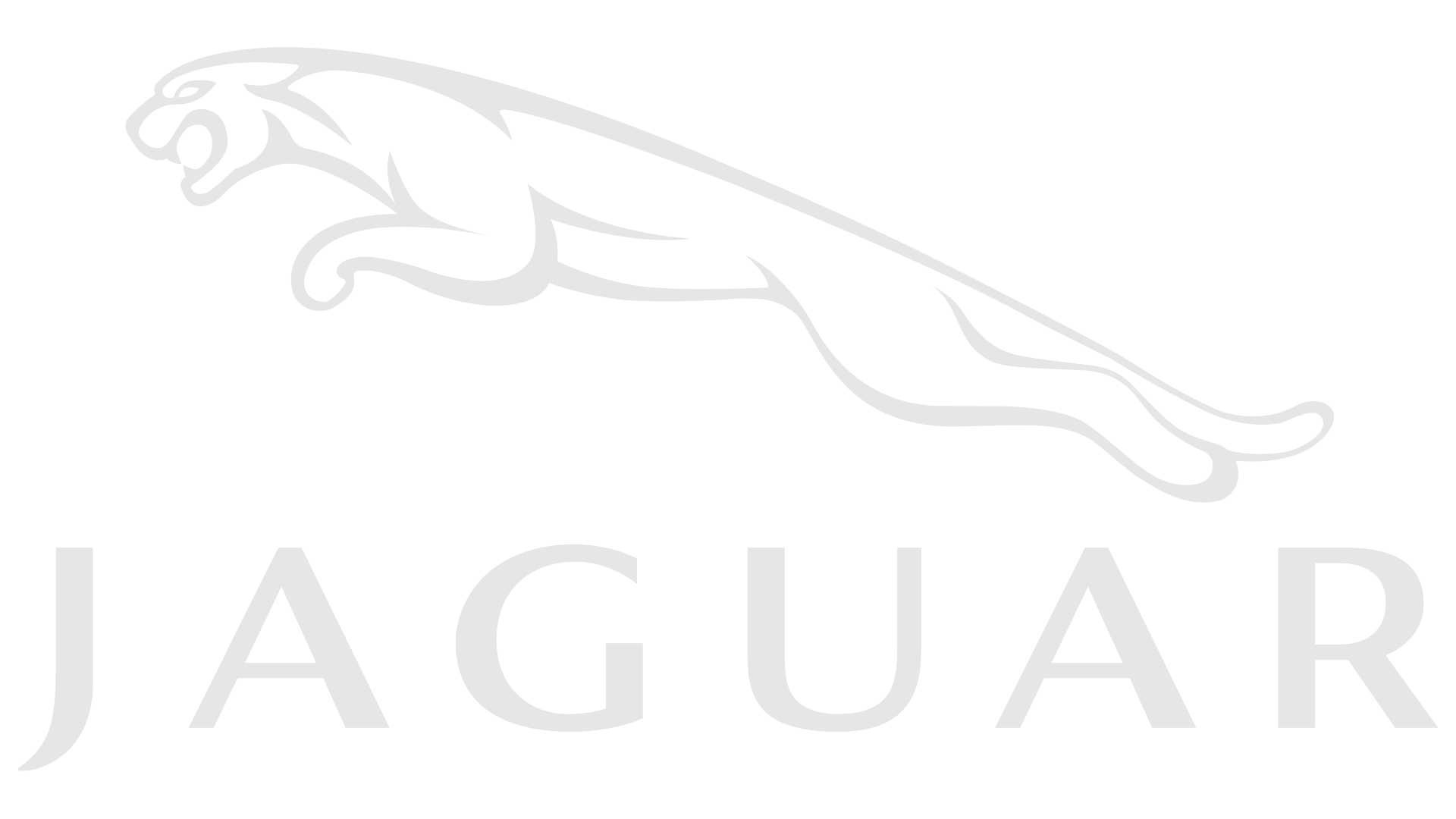
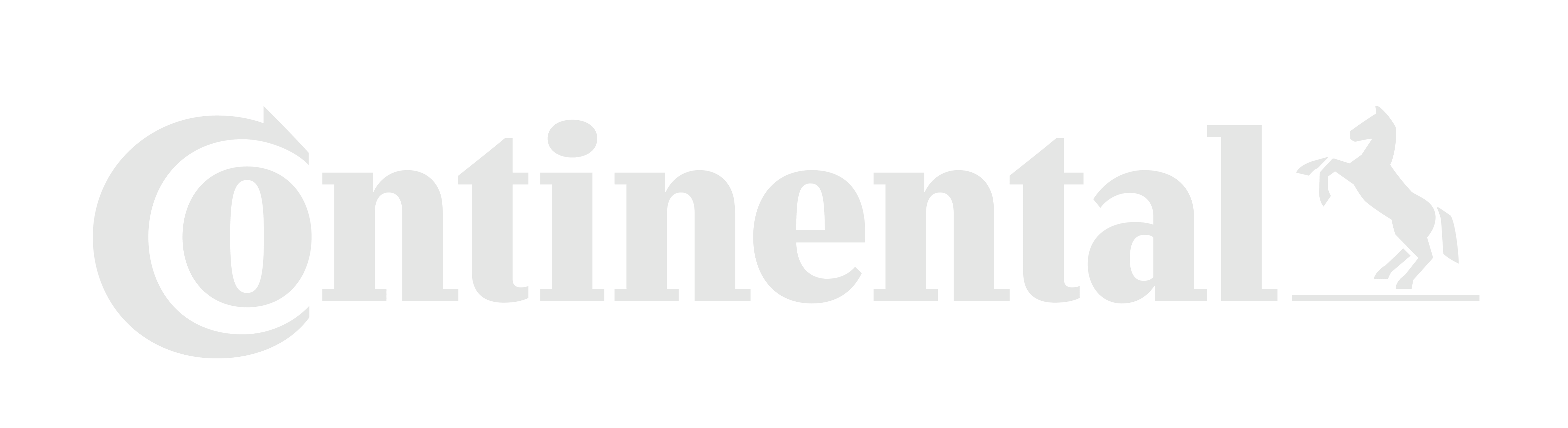
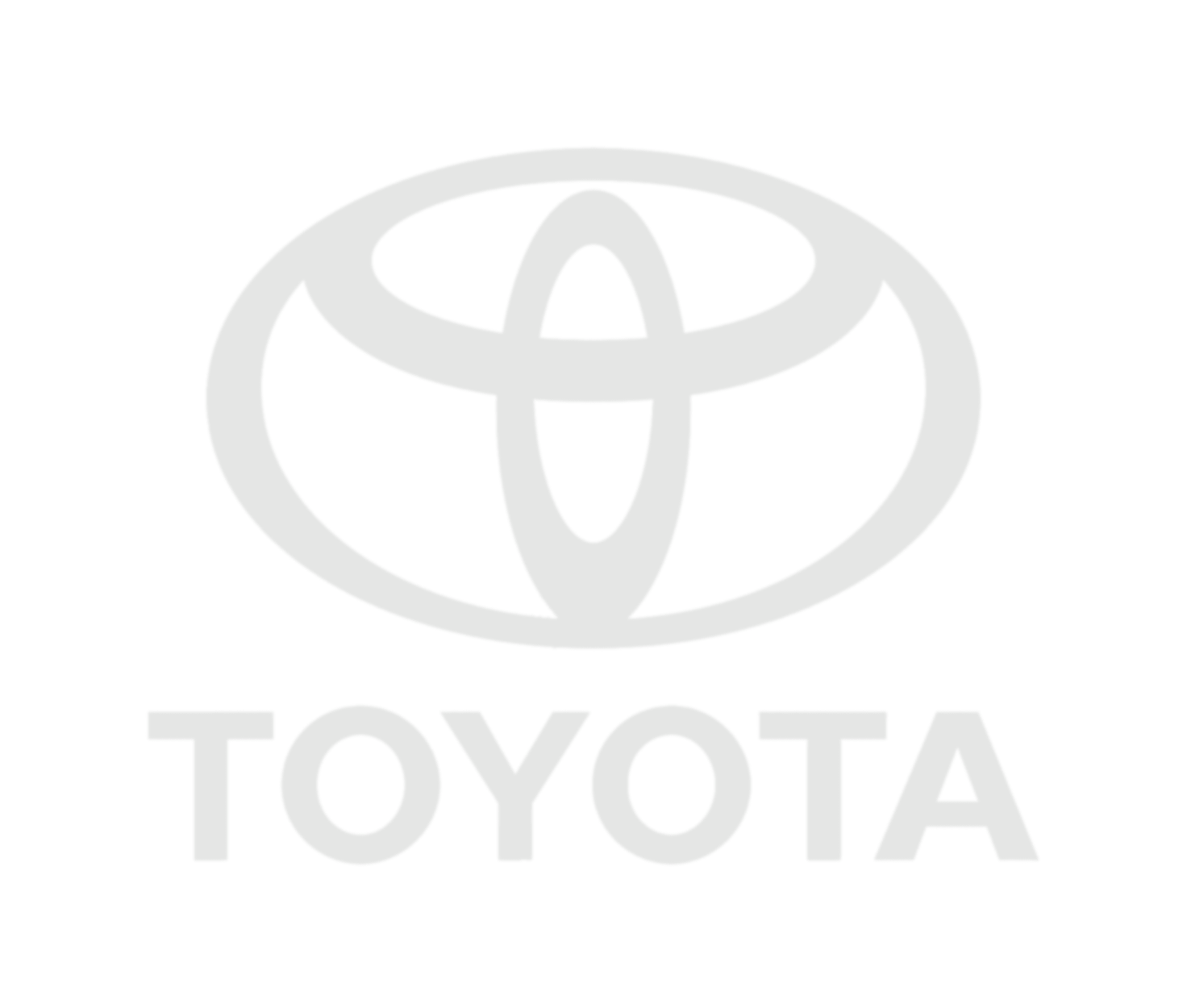
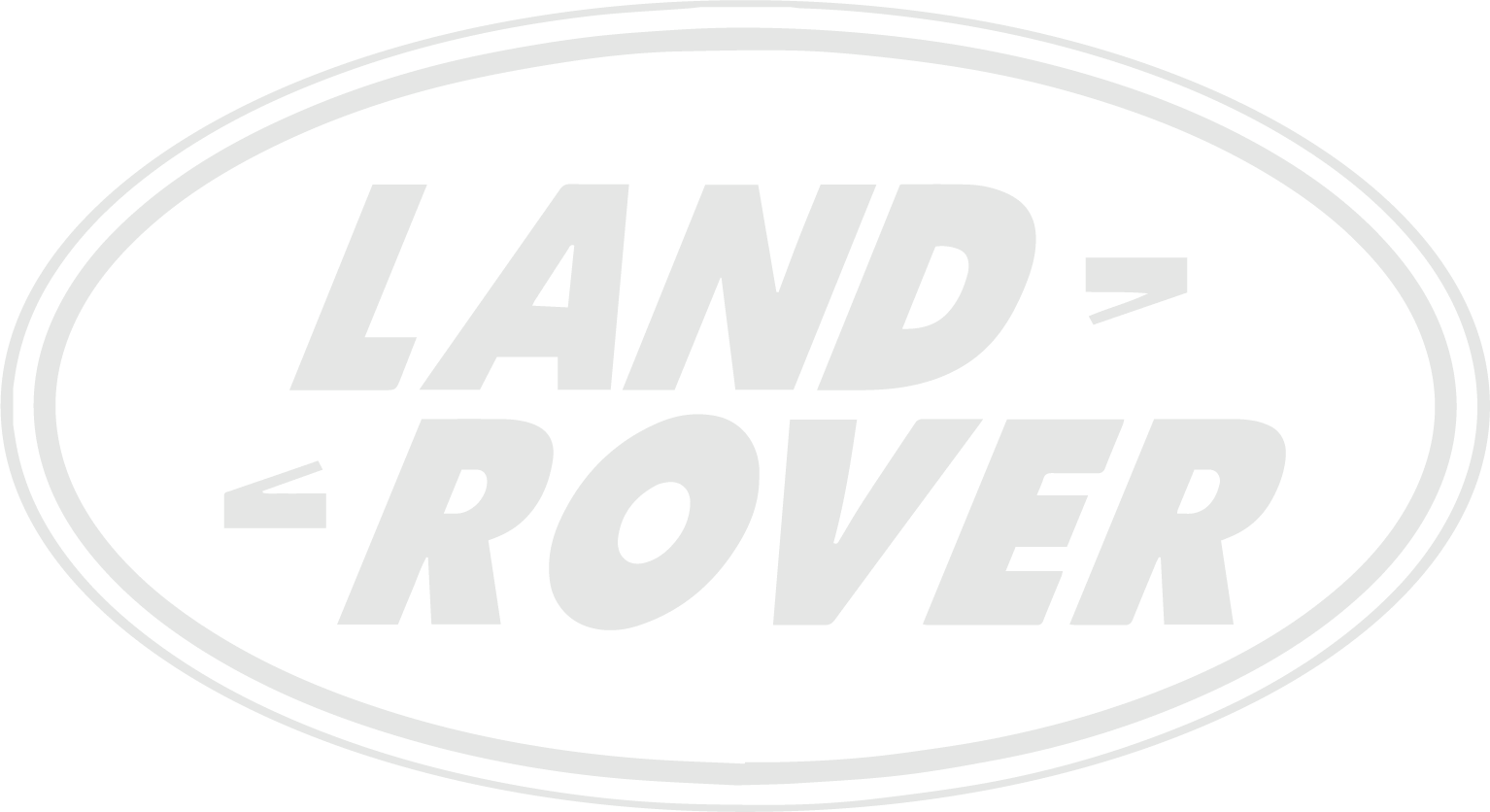
Where to use Dycem in Automotive
Entry and Exit to Cleanrooms
Outside Paint Booths
Small Components Areas
EV Battery Assembly
ESD Zones
Engine Laboratories
Display and Glass Manufacturing
Contamination: The Risk in the Automotive Industry
Automotive manufacturing requires various levels of cleanliness throughout the supply chain. As vehicles have advanced, so have their manufacturing and safety specifications. During the manufacturing process, sensitive components can become compromised by even slight changes in pressure, humidity, and temperature, and are especially vulnerable to contamination and the effects of static electricity. Automotive contamination control is required to ensure that all the components are manufactured free of flaws and carefully assembled to prevent the risk of product malfunctions.
Common types of contamination found within auto manufacturing include dust, debris, salts, minerals, static, metals, skin cells, and other particulate matter. Electrostatic Discharge (ESD) can also be a contaminant for devices with an electronic component. The presence of these contaminants can cause many negative outcomes including product quality defects, system failures, factory shutdowns, unsatisfactory customer audits, and recalls.
The risks to a company’s brand, its profitability, and its people are too great to be ignored. Effective contamination control is essential for facilities throughout fabrication, assembly, integration, and testing.
Dycem mats, implemented as part of a contamination control strategy, offer optimal support in reducing the risk of contamination in automotive manufacturing and finishing.
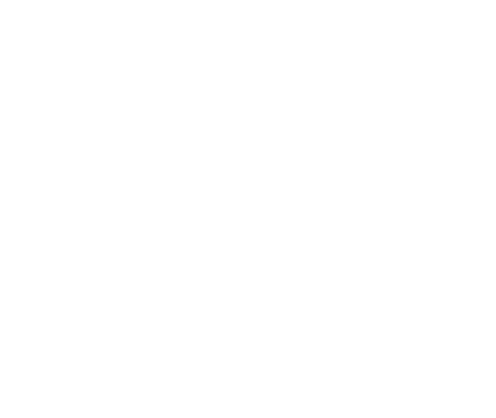
Don't Ignore the Floor...
80% of Contamination Enters a Critical Space at Floor Level.
Benefits of Dycem in the Automotive Industry
superior floor & Air particulate control
Dirt and dust are captured on Dycem mats and remain on the surface until cleaned off. With Dycem, automotive manufacturers benefit from a reduction in floor-level particulate of up to 99.9% and a reduction in air particulate levels of up to 75%.
ESD Protection for products & Processes
With Dycem mats installed prior to critical areas, our automotive customers have peace of mind that damage from an Electrostatic Discharge (ESD) occurrence will be minimized. All Dycem mats dissipate static at 10⁸ ohms.
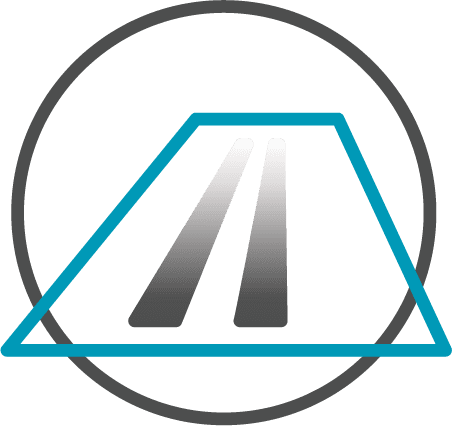
Support for Wheeled Traffic & Heavy Loads
Designed to withstand substantial weight of up to 1280 lb/in² (90 kg/cm²), Dycem Workzone allows automotive manufacturers to effectively decontaminate often unaddressed wheels with minimal downtime from labor-intensive and manual processes.
Our Products, Your Industry
Powertrain component production, systems integration and testing, paint shops, and finishing lines are all examples of areas throughout the automotive process that must be protected from contamination. Dycem has solutions to support the many vital steps in the manufacture of vehicles and their parts. Automotive contamination control in critical spaces and cleanrooms is our priority.
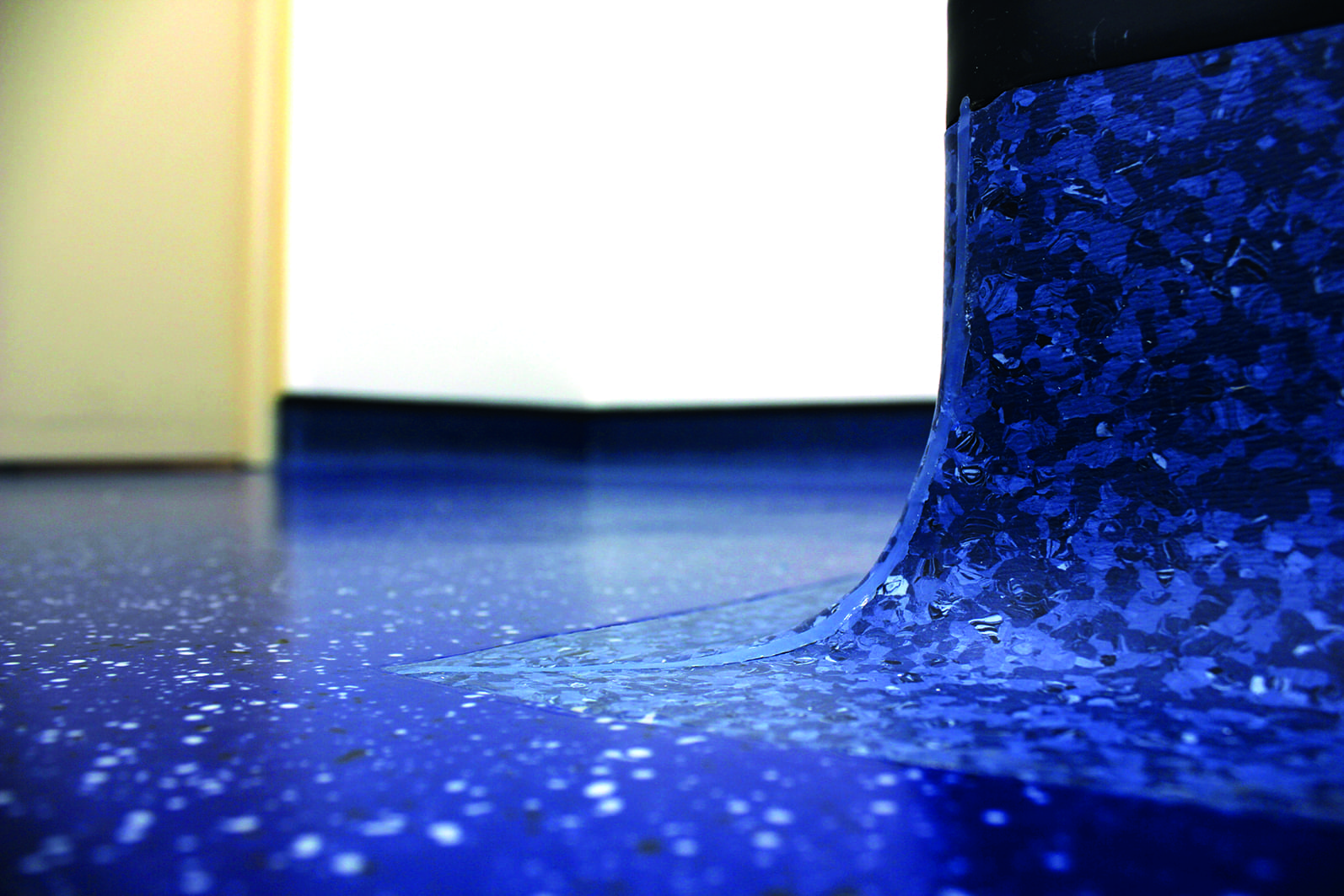
Dycem CleanZone
CleanZone helps control contamination from the shoes of personnel.
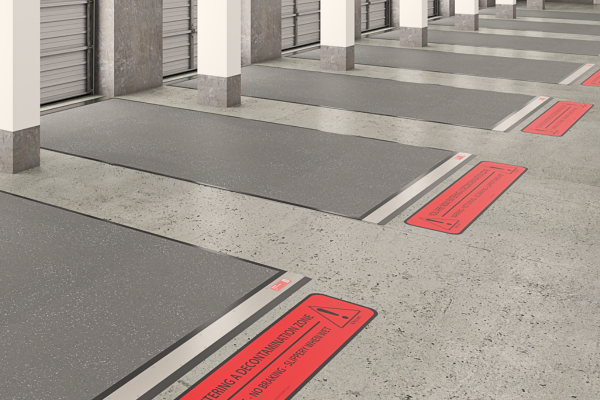
Dycem WorkZone
WorkZone is the only effective solution for decontamination of heavy wheels.
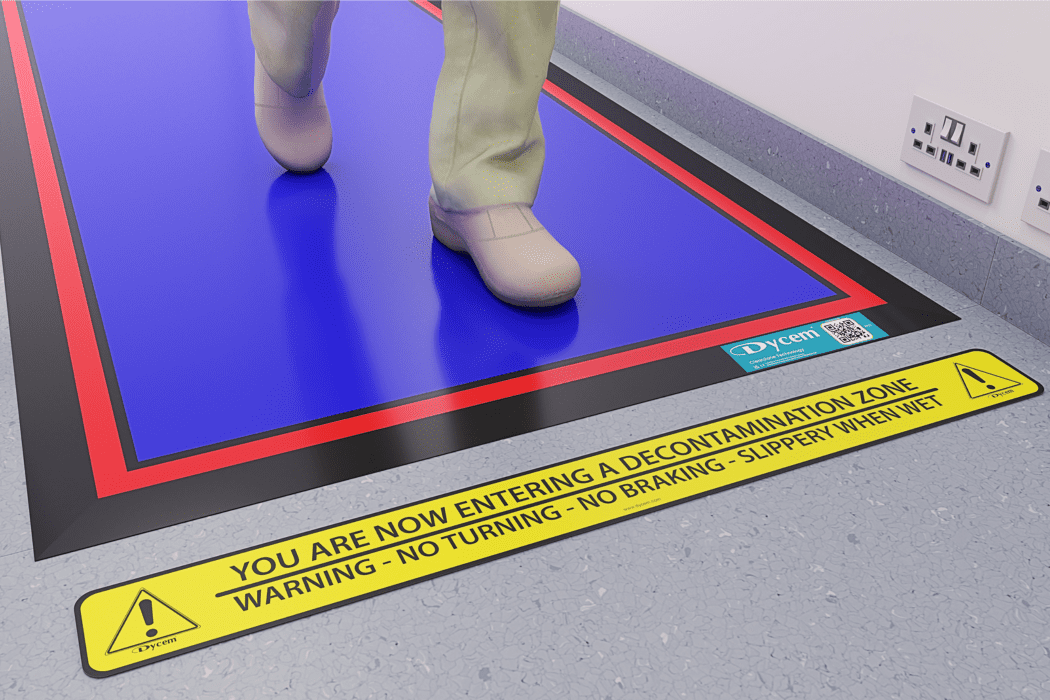
Dycem Floating Mats
Floating Mats are an automotive contamination control solution that can be moved as needed.
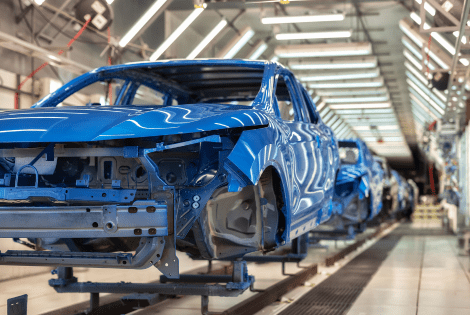
In Your Industry
Discover your industry’s specific applications—all conveniently summarized right here.
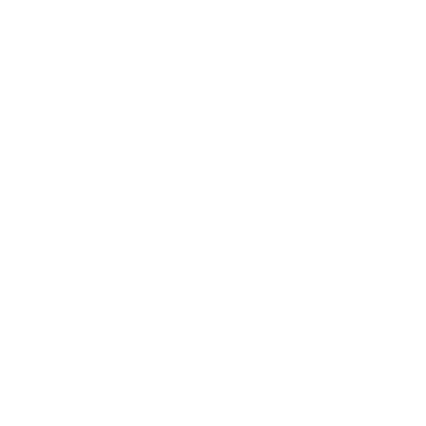
Success Stories...
Discover our success stories in your industry.
Learn how our customers have benefitted from installing Dycem.
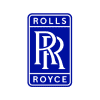
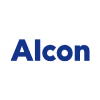
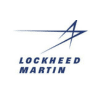
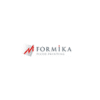
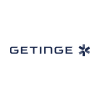
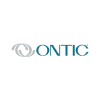
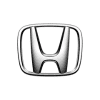

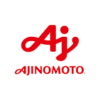
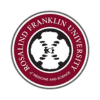
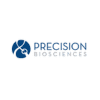
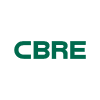
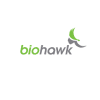
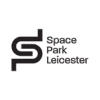
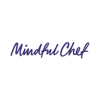
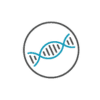
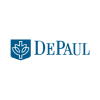
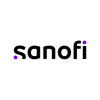
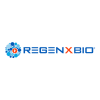
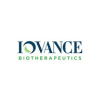
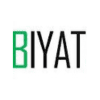
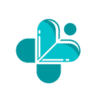
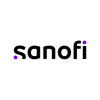
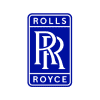
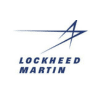
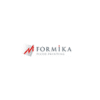
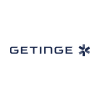
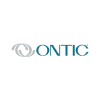
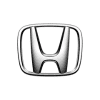

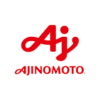
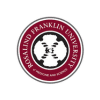
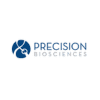
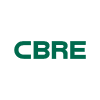
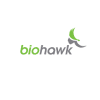
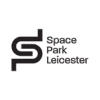
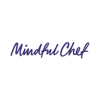
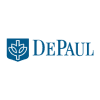
Automotive Quality Management System
Read the following section of the Automotive QMS Update IATF 16949:2016:
“8.5.4.1: Preservation – supplemental
- Adds specificity to preservation controls and includes application to internal and/or external providers.
- Preservation activities are expanded in two ways: first, activities that are considered preservation controls, and second, locations where preservation controls apply.
- Preservation controls include the preservation of identification during the product shelf life; a contamination control program appropriate to identified risks; design and development of robust packaging and storage areas; adequate transmission and transportation considerations; and measures to protect product integrity.
Section 8.7.1.7: Nonconforming product disposition - Strengthen the requirement of disposition of nonconforming product by clarifying that organizations must also have a documented process for disposition of nonconforming product not subject to rework or repair.
- Planned activities need to be managed and the results considered to improve this process.
- Automotive contamination control practices should be applied to avoid any risk of unintended use of this type of nonconforming products.
- Customer approval is required before nonconforming products in this category can be diverted for service or any other use.”